Scan Terminal scherm Afboeken Input P.O. (LOTSSTAG)
Vanaf heden is er een nieuw Scan Terminal scherm aan de bestaande reeks toegevoegd, en wel eentje t.b.v. het afboeken van grondstoffen van een Produktieorder, en wel op een zeer specifieke manier.
Het scherm is onderverdeeld in 2 Tabbladen. Op het eerste Tabblad scannen we de produktieorder alsmede de af te boeken partij, op het 2e tabblad geven we vervolgens te boeken verbruik aan.
Als voorbeeld onderstaande Omvorm Opdracht, waarin 80 dozen met daarin 6 zakken van 2½ Kg appels worden omgevormd uit kisten appels van 18 Kg.
Een doos van 6 zakken van 2½ Kg = 15 Kg, 80 dozen = 1200 Kg. Normaliter zouden we hiervoor dus 1200 Kg appelen nodig hebben, hetgeen (bij verbruik van kisten van 18 Kg) uitkomt op 66,6 kisten, hetgeen in dit voorbeeld bij het maken van de Omvorm Opdracht reeds is gewijzigd naar een input van 68 kisten.
Bij het afboeken van grondstoffen volgens dit Scan Terminal scherm, moeten we als eerste op Tabblad 1 de Produktieorderregel scannen waarop we goederen willen afboeken. De Produktieorderregel wordt geacht in Barkode te worden afgedrukt op de Produktieorder-print, en te bestaan uit
Produktieordernummer + Charge-/Serie + Regelnummer. Middels deze drie gegevens kunnen we een produktieorderregel identificeren. Zodra we de af te boeken PO-regel hebben gescand, worden de gegevens van die regel opgehaald en getoond.
Daarna moeten we de pallet scannen met daarop de af te boeken goederen. Zodra we dat gedaan hebben (uitgangspunt in deze situatie is dat een pallet met de benodigde Granny Smith appelen scannen) verschijnt het 2e scherm.
Default wordt hierbij voorgesteld om de hele partij (de hele pallet, waarvan iedere verschijningsvorm hetzelfde Subchargenummer behoort te hebben) in te steken. Bij de eerste pallet zal dit nog niet zo vreemd zijn, immers, het scherm toont dat we 1224 Kg nodig hebben, en gezien de inhoud van 18 Kg per kist zijn dat 68 Verschijningen (kisten). Er liggen 49 kisten op de gescande pallet, en dus kunnen we maximaal deze 49 kisten afboeken. Maar, kijken we naar de afboeking van de volgende pallet...
dan zien we dat het systeem nog steeds voorstelt om default een hele pallet met 49 kisten van 18 Kg te verbruiken, waar er maar 342 Kg verwacht nodig is, hetgeen uitkomt op 19 Verschijningen.
En, om het nog iets verwarrender te maken, hoewel we nu nogmaals 49 kisten x 18 Kg = 882 Kg afboeken, verbruiken we dit niet echt.
De truc is dat we via deze funktionaliteit alle verbruikte pallets volledig afboeken, en dat we achteraf, zodra de order gereed is, aangeven hoeveel er over is gebleven. Dit hoeven nl. geen 30 kisten (49 - 19) te zijn, immers, met dat de appels in zakken worden verpakt, worden meteen de 'rotte appels' er tussenuit gehaald. Natuurlijk geldt dat in werkelijkheid nog steeds voor 1200 Kg verpakte appelen ook 1200 Kg input nodig zal zijn, maar, 1200 Kg 'goede input', waar dit wel eens kan impliceren dat we misschien wel 1300 of 1400 kg moeten insteken (afhankelijk van de kwaliteit van de partij) om hier 1200 Kg goed produkt uit te kunnen halen. De hoeveelheid die overblijft kan door de gebruiker geteld worden, en kan via een separaat scherm worden teruggeboekt als korrektie op hetgeen via deze funktie teveel werd afgeboekt. Ofwel, stel dat we achteraf 26 kisten terugboeken, dan zal het werkelijke verbruik 49 kisten van de eerste partij + 49-26 = 23 kisten van de 2e pallet = 72 kisten zijn geweest. Deze 72 kisten bepalen de kostprijs van deze Produktieorder.
LET OP: Bovenstaande werkwijze impliceert dat de afgeboekte pallet met 49 kisten maar op één Produktiestation tegelijk verbruikt kan worden. Het mág dus niet zo zijn dat twee Produktiestations aan twee afzonderlijke Produktieorders werken, en beide voorraad afsnoepen van dezelfde pallet (immers, de 1e P.O. zal de hele partij al afboeken).
Hoewel het scherm bedoeld is voor bovenstaande situatie, is al wel meteen de flexibiliteit geboden om toch minder te registreren. Zo kan dus ook op voorhand al worden aangegeven dat er slechts 23 kisten ingestoken zijn, hetgeen het achteraf terugboeken overbodig maakt. Middels de buttons bovenin het 2e Tabblad kan voor de situatie worden gekozen welke het meest overeenkomt met de gewenste situatie:
- òf de hele pallet insteken (al dan niet gekombineerd met het achteraf terugboeken van het restant)
- òf we boeken het benodigd aantal verschijningen af
- òf we boeken het benodigd aantal eenheden af
Clicken we op de 2e button, dan zal het scherm wijzigen naar:
Zouden we in eenheden afboeken, dan zien we:
Het clicken op een van de buttons bepaalt enkel of we gaan afboeken o.b.v. Aantal Verschijningen danwel o.b.v. Aantal Eenheden, en of we dit doen o.b.v. het insteken van de hele partij (volle pallet) danwel het benodigd aantal eenheden. Nadat een keuze gemaakt is, kan de betreffende hoeveelheid alsnog worden aangepast, doch (uiteraard) nimmer meer dan hetgeen (vrij) op de pallet aanwezig is.
LET OP: Veel van de Scan Terminal funktionaliteit anticipeert op een werkwijze dat er een uniek (Sub-) Chargenummer wordt gegenereerd per Palletnummer. De Subcharge wordt daarbij uniek geacht, en dient identificerend te zijn voor het gehele Voorraaditem, d.w.z. de kombinatie Artikel, Verschijningsvorm, Charge, Interne Charge, Lokatie, Werkelijke-Inhoud en Kenmerken. Het Batchnummer is bij die situaties dus uniek in het hele systeem. Hieruit valt dan eigenlijk al meteen op te merken dat we bij dit soort produkten nimmer in eenheden mogen afboeken, immers, stel dat we 4 Kg zouden afboeken uit een kist van 18 Kg, dan houden we een kist van 14 Kg over, hetgeen t.o.v. de andere kisten van 18 Kg een nieuwe werkelijke inhoud wordt, en daarmee een 2e Voorraaditem, waar de regel juist is dat het Chargenummer slechts tot 1 Voorraaditem mag leiden.
Toch is de mogelijkheid opgenomen op deze wijze te kunnen afboeken, omdat niet alle produkten op bovenstaande manier (volle pallets) zullen worden afgehandeld. Neem bijv. maar eens de situatie dat we 6 appels op een schaaltje zouden produceren, en de receptuur dus 'schaaltjes' zal bevatten. Die schaaltjes zitten per 1000 in een doos, en er staan wellicht 80 dozen op een pallet. Als we 1 schaaltje nodig hebben zullen we dus nooit een hele pallet tegelijk willen afboeken.
De praktijk zal uitwijzen hoe hiermee te werken valt; desnoods t.z.t. middels aanvullend maatwerk uit te breiden tot een instelling waarmee kan worden aangegeven hoe er afgeboekt moet worden.
Middels een separaat Scan Terminal scherm kan de Output van de Produktieorder worden opgeboekt, en kan de Produktieorder worden afgesloten.
AlternatievenHet zal U wellicht niet ontgaan zijn dat het eerste scherm nog een Spinner control bevat. Deze heeft alles te maken met de mogelijkheid tot het werken met alternatieven.
Bij het produktieproces kan blijken dat de appels die verwerkt moeten worden, er niet (of niet meer) zijn. Zo kan op voorhand blijken dat er in deze situatie beter een andere kwaliteit (ander produkt) ingezet kan worden, danwel blijkt halverwege het produktieproces dat de appels op zijn, en op een alternatief moet worden overgestapt. Het overstappen op een alternatief kán door de Produktieorder worden afgedwongen, maar hoeft niet. In de Receptuur van een produkt (Produktie, niet omvorming) kan een alternatief worden opgenomen door deze direkt onder (kwa regelnummer) het gewenste produkt op te nemen
met een hoeveelheid van 0,000. Meerdere alternatieven zijn mogelijk, en zullen op de print van de Produktieorder worden afgedrukt.
Stel dat die Receptuur afdwingt dat een appel maat 113 een alternatief is voor een appel maat 100, dan hangt het er vervolgens weer vanaf hoe e.e.a. op het Scan Terminal scherm verwerkt wordt.
a. De gebruiker kan het alternatief (maat 113) op de Produktieorder scannen. In dat geval geeft ze met die scan al te kennen dat alternatief te willen inzetten. Zodra bij de 2e scan (het scannen van de voorraad) een ander produkt wordt gescanned dat het geselekteerde alternatief, zal een melding volgen; alleen het gescande alternatief zal mogen worden ingezet.
b. De gebruiker scant gewoon het hoofdprodukt (maat 100) maar gaat bij het rapen de klasse 113 afboeken. Het systeem konstateert dat er een ander produkt wordt gescanned t.o.v. het produkt wat op de gescande Produktieorderregel staat waarop dit moet worden afgeboekt, en meldt dit. Omdat het altijd kan zijn dat er per ongeluk een verkeerd etiket gescanned werd, wordt de vraag gesteld of het klopt dat er een ander produkt wordt ingezet. Is het antwoord op deze vraag Nee, dan kan een nieuwe partij worden gescanned, is het antwoord op deze vraag Ja, dan wordt de geplande hoeveelheid van de oorspronkelijke regel omgerekend naar het geplande verbruik van het gescande alternatief, hierbij rekeninghoudend met omrekeningsfaktoren tussen voorraadeenheden.
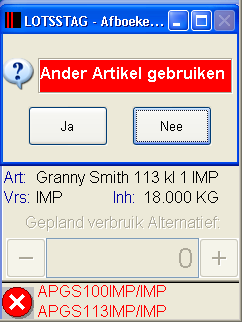
In het meldingen gedeelte van het Scan Terminal scherm (helemaal onderin) worden de Artikelnummers getoond van hetgeen gevraagd is, en hetgeen waardoor U dit gaat vervangen. Onder het scherm met de melding zal nog net de omschrijving leesbaar zijn van het geselekteerde alternatief.
Nb: Merk overigens op dat op deze wijze het ene artikel door een ander vervangen kan worden, doch dat U zelf bepaald wat wel/niet door elkaar vervangen kan worden. Technisch gezien zal het systeem niet het verschil weten tussen het vervangen van een appel met maat 100 door dezelfde appel maat 113, danwel het vervangen van diezelfde appel door een bloemkool.
Zodra bovengenoemde vraag met Ja beantwoord wordt, blijft het 1e Tabblad nog even aktief, en wordt aldaar het geplande verbruik berekend o.b.v. de regel die vervangen wordt, omgerekend naar de eenheid van het artikel welke als alternatief wordt ingezet.
Het geplande verbruik kan desgewenst aangepast worden (wellicht vereist het inzetten van een slechtere kwaliteit dat er gepland méér van moet worden ingestoken), waarna we alsnog met het afboeken verder kunnen gaan op het 2e Tabblad.
Nb: Indien op de Produktieorder het echte produkt werd gescand (1224 Kg nodig appels maat 100), dan laat deze hoeveelheid zich omrekenen naar de geplande hoeveelheid van het geselekteerde alternatief. Indien op de Produktieorder een alternatief gescand wordt, is het verhaal iets anders. Zoals gezegd wordt een regel als alternatief gezien zodra de hoeveelheid van die regel 0 is. En, 0 omrekenen naar iets anders zal niet echt helpen. Derhalve moeten een alternatief direkt onder het oorspronkelijke produkt worden opgenomen. Bij het scannen van een 0 regel op de Produktieorder, zal het Scan Terminal de Receptuur van die Produktieorder naar boven doorlopen vanaf de gescande regel. De eerst hogere regel waarbij wél een hoeveelheid is opgenomen, wordt dan geacht het produkt te zijn waarnaar verwezen wordt. Pas indien er geen regels boven dit regelnummer staan, wordt dezelfde koding uitgevoerd, maar dan op zoek naar regels onder de gescande regel.